- Do not open the housing: loaded spring.
- Hold MEMOLUB® down during manual checks
- Leq <70 dB
- Use MEMOLUB® only for greasing machinery
- Use only lubricant cartridges and batteries recommended by the manufacturer
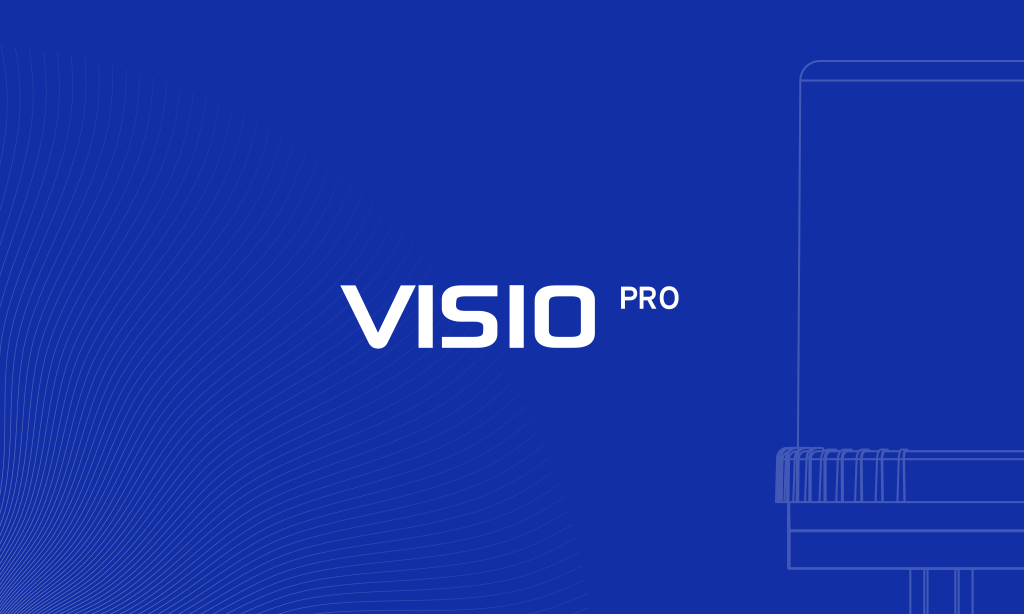
Memolub® Visio PRO User guide
Precautions
Dimensions
Standard
120cc I 4oz
Mega
240cc I 8.1oz
Giga
480cc I 16.2oz
OIL R-500
500cc I 16.9oz
Settings & Feedback
FREQUENCY SETTINGS
From serial numbers VPR-XX-XXXX
WHEEL POSITION | DOSING PERIODICITY | MAX. DAILY OUTPUT* | REFILLING FREQUENCY VS. CARTRIDGE CONTENT (120CC) | REFILLING FREQUENCY VS. CARTRIDGE CONTENT (240CC) | REFILLING FREQUENCY VS. CARTRIDGE CONTENT (480CC) |
---|---|---|---|---|---|
0 | External (PLC) | ||||
1 | 48 hours | 0.3cc/day | 12 months | 24 months** | 48 month** |
2 | 24 hours | 0.6 cc/day | 6 months | 12 months | 24 months** |
3 | 16 hours | 0.9 cc/day | 4 months | 8 months | 16 months** |
4 | 12 hours | 1.2 cc/day | 3 months | 6 months | 12 months |
5 | 8 hours | 1.8 cc/day | 2 months | 4 months | 8 months |
6 | 6 hours | 2.4cc/day | 1.5 month | 3 months | 6 months |
7 | 4 hours | 3.6 cc/day | 1 month | 2 months | 4 months |
8 | 2 hours | 7.2 cc/day | 0,5 month | 1 month | 2 months |
9 | 1 hour | 14.4 cc/day | 0,25 month | 0,5 month | 1 month |
*Maximum daily output without stroke washers.
**Please consider lubricant expiry date for long cartridge lifetimes.
FREQUENCY SETTINGS
For all other serial numbers
WHEEL POSITION | DOSING PERIODICITY | MAX. DAILY OUTPUT* | REFILLING FREQUENCY VS. CARTRIDGE CONTENT (120CC) | REFILLING FREQUENCY VS. CARTRIDGE CONTENT (240CC) | REFILLING FREQUENCY VS. CARTRIDGE CONTENT (480CC) |
---|---|---|---|---|---|
0 | External (PLC) | ||||
1 | 24 hours | 0.6 cc/day | 6 months | 12 months | 24 months** |
2 | 16 hours | 0.9 cc/day | 4 months | 8 months | 16 months** |
3 | 12 hours | 1.2 cc/day | 3 months | 6 months | 12 months |
4 | 8 hours | 1.8 cc/day | 2 months | 4 months | 8 months |
5 | 4 hours | 3.6 cc/day | 1 month | 2 months | 4 months |
6 | 2 hours | 7.2 cc/day | 0,5 month | 1 month | 2 months |
7 | 1 hour | 14.4 cc/day | 0,25 month | 0,5 month | 1 month |
8 | 1/2 hour | 28.8 cc/day | 4 days | 0,25 month | 0,5 month |
9 | 1/4 hour | 57.6 cc/day | 2 days | 4 days | 0,25 month |
*Maximum daily output without stroke washers.
**Please consider lubricant expiry date for long cartridge lifetimes.
VOLUME SETTINGS [cc/day]
From serial numbers VPR-XX-XXXX
NUMBER OF STROKE WASHERS* | WHEEL POSITION | |||||||||
---|---|---|---|---|---|---|---|---|---|---|
0 | 1 | 2 | 3 | 4 | 5 | 6 | 7 | 8 | 9 | |
0 | External (PLC) | 0.3 | 0.6 | 0.9 | 1.2 | 1.8 | 2.4 | 3.6 | 7.2 | 14.4 |
![]() |
External (PLC) | 0.28 | 0.56 | 0.84 | 1.12 | 1.69 | 2.24 | 3.4 | 6.7 | 13.5 |
![]() ![]() |
External (PLC) | 0.26 | 0.52 | 0.79 | 1.04 | 1.58 | 6.3 | 3.15 | 6.3 | 12.6 |
2 ![]() ![]() |
External (PLC) | 0.24 | 0.49 | 0.73 | 0.98 | 1.46 | 5.85 | 2.92 | 5.85 | 11.7 |
3 ![]() ![]() |
External (PLC) | 0.22 | 0.45 | 0.67 | 0.9 | 1.35 | 5.4 | 2.7 | 5.4 | 10.8 |
4 ![]() ![]() |
External (PLC) | 0.2 | 0.41 | 0.62 | 0.82 | 1.24 | 4.95 | 2.47 | 4.95 | 9.9 |
5 ![]() ![]() |
External (PLC) | 0.18 | 0.37 | 0.56 | 0.74 | 1.1 | 4.5 | 2.2 | 4.5 | 9 |
6 ![]() ![]() |
External (PLC) | 0.17 | 0.34 | 0.51 | 0.68 | 1 | 4.05 | 2.02 | 4.05 | 8.1 |
*The circlip must always be added on top of the washers.
VOLUME SETTINGS [cc/day]
For all other serial numbers
NUMBER OF STROKE WASHERS* | WHEEL POSITION | |||||||||
---|---|---|---|---|---|---|---|---|---|---|
0 | 1 | 2 | 3 | 4 | 5 | 6 | 7 | 8 | 9 | |
0 | External (PLC) | 0.6 | 0.9 | 1.2 | 1.8 | 3.6 | 7.2 | 14.4 | 28.8 | 57.6 |
![]() |
External (PLC) | 0.56 | 0.84 | 1.12 | 1.69 | 3.4 | 6.7 | 13.5 | 27 | 54 |
![]() ![]() |
External (PLC) | 0.52 | 0.79 | 1.04 | 1.58 | 3.15 | 6.3 | 12.6 | 25.2 | 50.4 |
2 ![]() ![]() |
External (PLC) | 0.49 | 0.73 | 0.98 | 1.46 | 2.92 | 5.85 | 11.7 | 23.4 | 46.8 |
3 ![]() ![]() |
External (PLC) | 0.45 | 0.67 | 0.9 | 1.35 | 2.7 | 5.4 | 10.8 | 21.6 | 43.2 |
4 ![]() ![]() |
External (PLC) | 0.41 | 0.62 | 0.82 | 1.24 | 2.47 | 4.95 | 9.9 | 19.8 | 39.6 |
5 ![]() ![]() |
External (PLC) | 0.37 | 0.56 | 0.74 | 1.1 | 2.2 | 4.5 | 9 | 18 | 36 |
6 ![]() ![]() |
External (PLC) | 0.34 | 0.51 | 0.68 | 1 | 2.02 | 4.05 | 8.1 | 16.2 | 32.4 |
*The circlip must always be added on top of the washers.
VISUAL FEEDBACK
From serial numbers VPR-XX-XXXX
COLOR | STATUS |
---|---|
|
The testrun has been activated through pushbutton. / The pumping cycle ran successfully. |
|
Battery low / Lubricant cartridge empty. |
|
The gear motor is damaged or broken. / The pipe may be clogged. |
VISUAL FEEDBACK
For all other serial numbers
COLOR | STATUS |
---|---|
|
The gearbox motor is damaged or broken. The tube might be clogged. |
|
The battery is low. |
|
Abnormal temperature is detected or there is an issue with the pump. |
|
The testrun activation via the touchpad was successful. |
REMOTE INSTALLATION DISTANCES
TYPE OF INSTALLATION | MAXIMUM DISTANCE |
---|---|
Single point | 10m |
Multipoint with 2 outlets | 6m |
Multipoint with 4 outlets | 6m |
The settings above may evolve with the model version and are given for the current production. Please double-check with the supplied hard-copy documentation.
Specifications
Electric Specifications
MEMOLUB® VISIO | |
---|---|
Power Source | External Power Supply | Internal Battery |
Voltage | 24V DC/AC | 4.5V DC (3x1.5V DC AA) |
Short circuit protection | Yes |
Stroke duration | 8 seconds |
8 seconds | 15 minutes |
INSIDE THE BOX

MEMOLUB® VISIO EP Pump

MEMOLUB® Housing Kit

MEMOLUB® VISIO EP Base
INSTALLATION GUIDELINES
DIRECT INSTALLATION
-
1
Prime lube point and remove nipple.
-
2
Screw in the base using a strong threadlocker.
-
3
Pick the desired dosing setting.
-
4
Align the pin of the module with the notch of the base.
-
5
Screw tightly keeping the assemly aligned.
-
6
Connect the power plug.
-
7
Device initializes, flashes each color on, and makes one expulsion.
REMOTE INSTALLATION
-
1
Prime lube point and remove nipple.
-
2
Secure the mounting bracket.
-
3
Install the base and F1/4 fitting using a strong threadlock.
-
4
Screw BSP 1/8 fitting.
-
5
Cut hose to required size.
-
6
Insert hose into the lubrication point’s quick fitting.
-
7
Pick the desired dosing setting.
-
8
Align the pin of the module with the notch of the base.
-
9
Screw tightly keeping the assembly aligned.
-
10
Insert hose into the mounting bracket’s quick fitting.
-
11
Device initializes, flashes each color on, and makes one expulsion.
DISTRIBUTOR BLOCK INSTALLATION
-
1
Prime lube point and remove nipple.
-
2
Secure the mounting bracket.
-
3
Install the base and F1/4 fitting using a strong threadlock.
-
4
Screw BSP 1/8 fitting.
-
5
Cut the hoses to required size.
-
6
Insert the hoses into the lubrication point quick fittings.
-
7
Pick the desired dosing setting.
-
8
Align the pin of the module with the notch of the base.
-
9
Screw tightly keeping the assembly aligned
-
10
Insert hoses into the mounting bracket’s quick fitting.
-
11
Device initializes, flashes each color on, and makes one expulsion.
CARTRIDGE REPLACEMENT GUIDELINES
-
1
Disconnect power plug.
-
2
Remove VISIO EP Module from VISIO EP base.
-
3
Open VISIO EP Module (fingers on ribs).
-
4
Prime VISIO EP pump.
-
5
Insert new battery pack and seal. NOTE: the battery seal can be removed for 480cc cartridges
-
6
Squeeze air out of the cartridge.
-
7
Replace the cartridge on VISIO EP pump.
-
8
Close and lock VISIO EP Module (fingers on ribs).
-
9
Align the pin of VISIO EP Module with the notch of VISIO EP Base.
-
10
Screw tightly keeping the assembly aligned.
-
11
Connect power plug.
-
12
VISIO EP initializes, flashes each color on, and makes one expulsion. Green lights confirm normal operation.
Cable
6 DIN x 0.25 cable with female connector.
- Status output - (TO PLC IN)
- Status output + (TO PLC VCC)
- Power supply + (12/24VAC/DC)
- External input IN+ (FROM PLC OUT)
- External input IN- (FROM PLC GND)
- Power supply - (0VDC)
REMOTE CONTROL
INTERMITTENT MODE
DESCRIPTION | SIGNAL |
---|---|
INPUT SIGNAL (FROM CUSTOMER PLC/TIMER) |
![]() |
OUTPUT SIGNAL "BUSY" (TO CUSTOMER PLC) |
![]() |
PUMP OUTLET (TO LUBRICATION) |
![]() |
OUTPUT SIGNAL "DEFAULT" (TO CUSTOMER PLC) |
![]() |
CONTINUOUS MODE
DESCRIPTION | SIGNAL |
---|---|
INPUT SIGNAL (FROM CUSTOMER PLC/TIMER) |
![]() |
OUTPUT SIGNAL "BUSY" (TO CUSTOMER PLC) |
![]() |
PUMP OUTLET (TO LUBRICATION) |
![]() |
OUTPUT SIGNAL "DEFAULT" (TO CUSTOMER PLC) |
![]() |
WIRING EXAMPLE
Here you have a wiring example with feedback from limit switch. For other examples please get in touch with your local distributor.
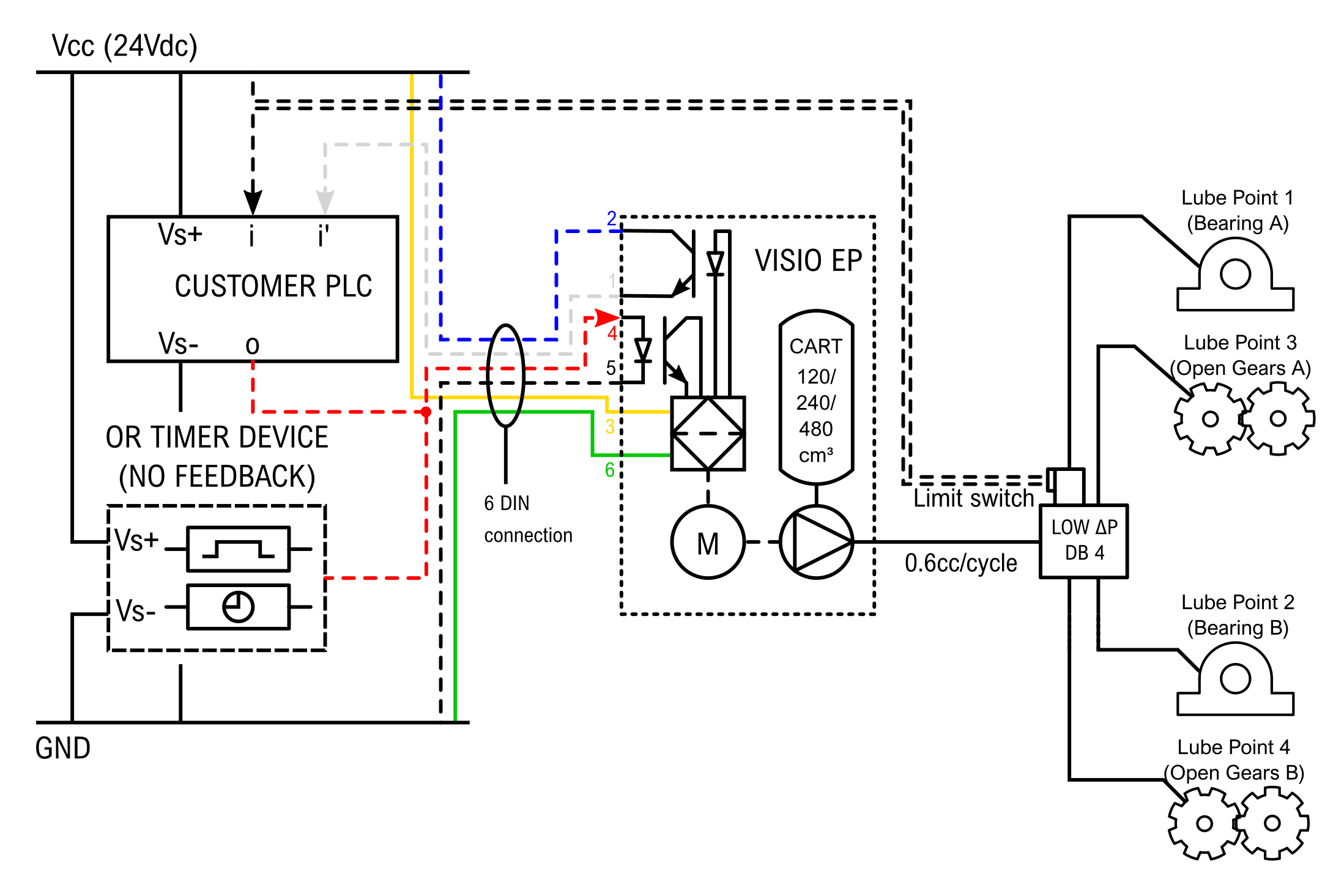
INSTALLATION GUIDELINES
Single point installation (direct)
-
1
Prime lube point and remove nipple.
-
2
Install VISIO EP Base on lube point using threadlocker (BSP 1/4).
-
3
With setting key, choose wheel position according to "Settings" table above.
-
4
Align the pin of VISIO EP Module with the notch of VISIO EP Base.
-
5
Screw tightly keeping the assembly aligned.
-
6
Connect power plug.
-
7
VISIO EP initializes, flashes each color on, and makes one expulsion. Green lights confirm normal operation.
Single point installation (remote)
-
1
Prime lube point and remove nipple.
-
2
Secure bracket.
-
3
Install VISIO EP base and F1/4 fitting on bracket using a strong threadlocker.
-
4
Install BSP 1/8 fitting on lube point.
-
5
Cut hose to required size.
-
6
Insert hose into bracket's quick fitting.
-
7
Insert hose into lube point's quick fitting.
-
8
With setting key, choose wheel position according to "Settings" table above.
-
9
Align the pin of VISIO EP Module with the notch of VISIO EP Base.
-
10
Screw tightly keeping the assembly aligned.
-
11
Connect power plug.
-
12
VISIO EP initializes, flashes each color on, and makes one expulsion. Green lights confirm normal operation.
Multi-point installation
-
1
Prime lube point and remove nipple.
-
2
Secure bracket.
-
3
Install VISIO EP Base on bracket using a strong threadlocker.
-
4
Install BSP 1/8 fitting on lube point.
-
5
Cut hoses to required size.
-
6
Insert hoses into bracket's quick fittings.
-
7
Insert hoses into lube points' quick fittings.
-
8
With setting key, choose wheel position according to "Settings" table above.
-
9
Align the pin of VISIO EP Module with the notch of VISIO EP Base.
-
10
A) Screw tightly keeping the assembly aligned. B) If necessary unscrew the union fitting under the bracket, move the connector on the left, and rescrew the union fitting..
-
11
Connect power plug.
-
12
VISIO EP initializes, flashes each color on, and makes one expulsion. Green lights confirm normal operation.
Touchpad Check Function
-
1
Locate the green triangular label indicating touchpad
-
2
Keep your fingers under VISIO EP Base, below the triangular sign. Blinking of the 4 green lights confirm activation of the touchpad.
-
3
Once the total touch duration has reached 5 sec, the 4 green lights are turned on simultaneously for 1s.
-
4
VISIO EP initializes, flashing each color on successively.
-
5
VISIO EP makes 1 expulsion.
-
6
After scanning all parameters, VISIO EP flashes green lights in case of normal operation. For any other colors, please refer to the FAQ section.
LEARNING PERIOD
The VISIO PRO is equipped with machine learning capabilities, allowing to take into account the environmental conditions in the status computation. There is a learning period of 20 cycles during which the lubricator must keep in the same environment, with no change in position, fastening, support or grease type. Should there be any modification of these parameters, the learning process can be redone by pushing on the pushbutton for more than 5 sec.
FAQ
-
What to do if nothing happens after screwing the module on the base?
- The pin of the module is possibly not proper aligned with the notch of the base. Unscrew the module from the base, align correctly and screw it again.
- VISIO EP Module is not tightly screwed to VISIO EP base. Turn it clockwise until stop.
- If battery-powered, there is possibly no battery inside the module or batteries are too low. Insert 3x 1,5 VDC AA new batteries to resolve the issue
- If externally powered, the base is not plugged to the power supply. Connect the base to the power cable (See "Cable" above). Check the power supply voltage & current (min 12V - 1A) and the wiring continuity.
- There is possibly something obstructing the communication between the base and the module contacts. Unscrew the module from the base, remove any dust or obstacles from the base and the module contacts and screw back together tightly.
-
What to do if the touchpad does not work after initialisation was completed successfully?
Your MEMOLUB® VISIO EP possibly initialised in an unstable environment. Unscrew the base from the module and screw again to reset the system. Wait until one expulsion is performed and you observe green lights, indicating the initialization is complete.
-
Why are the red lights blinking periodically?
- There is possibly a too high back pressure present in the system. Inspect your downstream piping to remove any clogging or jam. Activate the touchpad and check for at least 2 expulsions if the systems operate fine.
- There is possibly something obstructing the communication between the base and the module contacts. Unscrew the module from the base, remove any dust or obstacles from the base and the module contacts and screw back together tightly.
- The motor is broken. Replacement of the module is necessary.
- There is possibly a too high back pressure present in the system. Inspect your downstream piping to remove any clogging or jam. Activate the touchpad and check for at least 2 expulsions if the systems operate fine.
-
Why are the yellow lights blinking periodically.
There is possibly something obstructing the communication between the base and the module contacts. Unscrew the module from the base, remove any dust or obstacles from the base and the module contacts and screw back together tightly. If nothing improves, the batteries are empty. Replacement of the battery pack is necessary.
-
Why are the blue lights blinking periodically.
- The cartridge is possibly out of grease. Replacement of the cartridge is necessary.
- The system is not primed. Prime the system using a manual grease pump.
- The system is operating out of its minimum and maximum temperature range. Please make sure the system is operating within the recommended temperature range.
- The cartridge is possibly out of grease. Replacement of the cartridge is necessary.
REGULATORY INFORMATION
SYMBOL | DECRIPTION |
---|---|
|
This product is compliant with Directives 2006/42/EC (Machinery). The relevant Declaration of Conformity is available here. |
|
This product is compliant with UK regulations 2008 No. 1597 (Supply of Machinery). The relevant Declaration of Conformity is available here. |
|
This product is compliant with customs union technical regulation TR CU 010/2011 (safety of machines and equipment). The relevant Declaration of Conformity is available here. |
|
The WEEE symbol is attached to the product in compliance with the EU directive 2012/19/EU on Waste Electrical and Electronic Equipment (WEEE). It is intended to deter the improper disposal of this product and to promote reuse and recycling. |
|
The packaging material can be recycled. Please arrange for the environmental appropriate disposal of the packaging. |